So much of being a practicing audio engineer is critical listening. So many times I hear other engineers talking about input signal, differences in gear, and how to deal with the artists, but I almost never hear about different techniques on sound absorption properties and room reflections.
Think about it, if this job relies so heavily on our ears, wouldn’t it be rather important to spend some time training our ears and studying the millions of characteristics that make the room you are monitoring in sweet or dissonant? Well, in this blog post we will spend some of that critically important time on this very topic.
Believe it or not, almost all materials have some sound absorbing properties. Incident sound energy that is not absorbed must be reflected, transmitted, or dissipated.
According to Merriam-Webster, a coefficient is a number that serves as a measure of some property or characteristic as of a substance, device, or process. It can also mean any of the factors of a product considered in relation to a specific factor; especially a constant factor of a term as distinguished from a variable. Wow, that is a brain full isn’t it? Well, a material’s sound absorbing properties can be described as a sound absorption coefficient in a particular frequency range. As audio engineers we deal with said coefficients on both sides of our input stage and in every task in the studio. There is an obvious correlation of numbers where complete absorption is 100% and 1 % is very minimal absorption. This means 100% is an almost completely “dead” room, while an absorption factor of 1% will have lots of reflections zipping around the sound field. Incident sound striking a room surface yields sound energy comprising reflected sound, absorbed sound and transmitted sound.
A good sound reflector will prevent sound transmission by forming a solid, impervious barrier and tend to be massive. Most good sound absorbers transmit sound and are typically porous, lightweight material. Taking this basic thought into the practice arena, this is why sound transmitted between rooms is hardly affected by adding sound absorption to a wall surface. When talking about sound absorbers there are three basic categories: porous materials typically made of matted or spun fibers, panel or membrane absorbers having an impervious surface mounted over an airspace, and resonators usually made by created holes or slots connected to an enclosed volume of trapped air. Don’t forget, the effectiveness of the above absorbers will dramatically change according to the mounting method you use.
Porous absorbers are commonly made from carpet, draperies, spray-applied cellulose, aerated plaster, and wool or glass fiber.
Most all of these materials will allow air to flow into their cellular structure where sound energy is converted to heat. Remember the Law of Conservation of Energy from Physics class, “energy is neither created nor destroyed.” The thickness of the porous material also plays an integral part to its absorptive factor. If there is a thin layer on a hard surface it will not make an efficient sound absorber. However, thicker materials will provide more bass sound absorption or damping. This is why most bass traps you see in the corners of a room will be made out of such porous materials.
Panel absorbers are non-rigid, non-porous materials that are placed over an airspace that vibrates in a flexural mode in response to sound pressure exerted by adjacent air molecules.
These absorbers include thin wood paneling over framing, lightweight impervious ceilings and floors, glazing and other large surfaces capable of resonating in response to sound. These types are most efficient in absorbing low frequencies. You will see this mostly used in orchestral applications where thin wood paneling traps most of the bass sound. If you need to remove some warmth from a room, this is the way to go.
Lastly, resonators typically absorb sound in a more narrow frequency range.
These include perforated materials and other materials that have openings like holes and slots. One classic type is the Helmholtz resonator. By the way, if you have ever encountered the dreaded cicada, their abdomen closely resembles this type of resonator and that is how they make that ear-piercing hum when they grace us every thirteen years. For those of you who have never seen or heard a cicada, this resonator is shaped like a bottle. The resonant frequency is commanded by the size of the opening, the length of the neck and the volume of air trapped in the chamber. Just like when you were a kid and blew into the top of a glass pop bottle and it makes that distinct drone. These resonators typically only absorb the mid-range frequencies unless you take very special care to design the face to be as acoustically transparent as possible. Slotted resonators usually have very similar acoustic response. If you lengthen the slots you can absorb some low frequencies so pay close attention to rooms with long-slotted resonator absorbers. Especially in music production, you don’t want to kill the low end because you will most definitely over compensate in the mix later.
I hope this has cleared up some confusion about room acoustics and the proper way to treat each type of problem you will face. As we all know, nothing is certain in the audio industry. There are an infinite number of possibilities including the weather and percentage of humidity in the room you are treating. I know of a great studio owner and audio engineer who purchased his own electrical transformer and pole to put it on. This resulted in a 10dB quieter studio than any other in town. I know we are not talking about cleanliness of electricity this time, but you get my point. The best thing to do before spending money and time treating a room is to do some preliminary research and talk to lots of more experienced persons than you. If you enjoyed this blog please contact me and let me know. If you love The Summing Amp, pass the joy along to ten of your friends or colleagues. This will help us grow and bring you more interesting and informative blogs in the future. Until next time…
If you want to read more about sound absorption check out the sites I like to read:
www.mixonline.com
www.soundonsound.com
www.aes.com
Saturday, July 23, 2011
Sunday, July 10, 2011
The Legendary, Bill Putman
How many engineers out there have used any of the listed: echo chambers, multi-band eq’s, the 1176, Universal recording consoles, or any UREI products? Well, let me answer that question, tons of us!
For those of you still in the dark about Universal Recording Electronics Industries (UREI), brought to us by “the father of modern recording,” Milton Tasker “Bill” Putnam. Born in 1920, Bill was a well-respected audio engineer, songwriter, producer, studio designer and businessman who is responsible for most of the tools we all use to produce pro-level recording sessions. Bruce Swedien, engineer on Michael Jackson’s “Thriller” and former colleague of Bill’s described his achievements by saying, “Bill Putnam was the father of recording as we know it today. The processes and designs which we take for granted – the design of modern recording desks, the way components are laid out and the way they function, console design, cue sends, echo returns, multitrack switching – they all originated in Bill’s imagination.” (mixonline, 2007)
Universal Recording in Chicago, one of America’s first independent recording studios, was founded by Bill in the 1950’s and quickly grew a reputation by recording such artists as Patti Page, Vic Damone, Duke Ellington, Count Basie, Sarah Vaughan, Little Walter, and Dinah Washington.
During this period, Universal had a number of firsts, including the first use of tape repeat, the first vocal booth, the first multiple voice recording, one of the first to use 8-track recording, the first use of delay lines in the studio, and the first release of half-speed mastered discs. (mixonline 2007) By the mid-1950’s, Putnam was one of the most sought-after engineer-producers in the United States, Universal Recording subsequently became so successful that clients, including the great Quincy Jones, began urging him to open a facility on the west coast. In the late 50’s, he sold his interest in Universal Recording and with support from Frank Sinatra and Bing Crosby established United Recording Corp. and moved to Hollywood. He began to utilize his new technologies and inventions into the new facility, expanding and re-designing the existing studios, incorporating much larger studio control rooms.
Bill was known to have tremendous foresight, in the early days when Universal Recording was founded, stereo recording was still very new and not widely excepted for major releases. Bill did however see the importance and at his own expense, he began making simultaneous stereo mixes of recordings produced at United Western and stockpiled these recordings. In the early 60’s when stereo was taking off as a consumer audio format, major labels found themselves without any back catalog of stereo recordings. This placed Putnam in the most advantageous position. Cleverly, Putnam charged for the (much more expensive) studio time used in the mixing of the stereo versions. Allen Sides, Putnam’s former partner said at the time the studio was bringing in around $200,000 per month in studio billing. In 1961, Putnam acquired Western Recorders on Sunset Boulevard, remodeled it and incorporating it into his existing complex, which he then renamed, united Western Recorders. In 1985, Putnam sold the studio to his partner Allen Sides, who then renamed it Ocean Way Recording, this is the one most people know about. There is no doubt, without Bill Putnam we wouldn’t make music the same way we have grown so accustom to. His genus is what has fueled the imaginations of many generations of engineers and even more to come in the future.
I hope this has given you some insight on where this industry has come from. If you didn’t know about Bill Putnam before reading this blog, hopefully you now know about the brilliance, ingenuity, and gusto that propelled one man at the speed of sound, on the crest of a foreign swell, barreling toward the unknown.
If you want to read more about Bill Putnam, go check out the sources I did at:
http://mixonline.com/recording/business/audio_bill_putnam_2/
http://www.freebase.com/view/en/bill_putnam
http://www.uaudio.com/about/our-story
Pictures from www.uaudio.com, 2011
For those of you still in the dark about Universal Recording Electronics Industries (UREI), brought to us by “the father of modern recording,” Milton Tasker “Bill” Putnam. Born in 1920, Bill was a well-respected audio engineer, songwriter, producer, studio designer and businessman who is responsible for most of the tools we all use to produce pro-level recording sessions. Bruce Swedien, engineer on Michael Jackson’s “Thriller” and former colleague of Bill’s described his achievements by saying, “Bill Putnam was the father of recording as we know it today. The processes and designs which we take for granted – the design of modern recording desks, the way components are laid out and the way they function, console design, cue sends, echo returns, multitrack switching – they all originated in Bill’s imagination.” (mixonline, 2007)
Universal Recording in Chicago, one of America’s first independent recording studios, was founded by Bill in the 1950’s and quickly grew a reputation by recording such artists as Patti Page, Vic Damone, Duke Ellington, Count Basie, Sarah Vaughan, Little Walter, and Dinah Washington.
During this period, Universal had a number of firsts, including the first use of tape repeat, the first vocal booth, the first multiple voice recording, one of the first to use 8-track recording, the first use of delay lines in the studio, and the first release of half-speed mastered discs. (mixonline 2007) By the mid-1950’s, Putnam was one of the most sought-after engineer-producers in the United States, Universal Recording subsequently became so successful that clients, including the great Quincy Jones, began urging him to open a facility on the west coast. In the late 50’s, he sold his interest in Universal Recording and with support from Frank Sinatra and Bing Crosby established United Recording Corp. and moved to Hollywood. He began to utilize his new technologies and inventions into the new facility, expanding and re-designing the existing studios, incorporating much larger studio control rooms.
Bill was known to have tremendous foresight, in the early days when Universal Recording was founded, stereo recording was still very new and not widely excepted for major releases. Bill did however see the importance and at his own expense, he began making simultaneous stereo mixes of recordings produced at United Western and stockpiled these recordings. In the early 60’s when stereo was taking off as a consumer audio format, major labels found themselves without any back catalog of stereo recordings. This placed Putnam in the most advantageous position. Cleverly, Putnam charged for the (much more expensive) studio time used in the mixing of the stereo versions. Allen Sides, Putnam’s former partner said at the time the studio was bringing in around $200,000 per month in studio billing. In 1961, Putnam acquired Western Recorders on Sunset Boulevard, remodeled it and incorporating it into his existing complex, which he then renamed, united Western Recorders. In 1985, Putnam sold the studio to his partner Allen Sides, who then renamed it Ocean Way Recording, this is the one most people know about. There is no doubt, without Bill Putnam we wouldn’t make music the same way we have grown so accustom to. His genus is what has fueled the imaginations of many generations of engineers and even more to come in the future.
I hope this has given you some insight on where this industry has come from. If you didn’t know about Bill Putnam before reading this blog, hopefully you now know about the brilliance, ingenuity, and gusto that propelled one man at the speed of sound, on the crest of a foreign swell, barreling toward the unknown.
If you want to read more about Bill Putnam, go check out the sources I did at:
http://mixonline.com/recording/business/audio_bill_putnam_2/
http://www.freebase.com/view/en/bill_putnam
http://www.uaudio.com/about/our-story
Pictures from www.uaudio.com, 2011
Subscribe to:
Posts (Atom)
Subscribe Now
Subscribe via email
Who is Mike Lancaster?
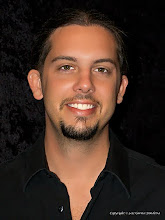
- Mike Lancaster
- I am a drummer and percussionist with twenty-three years experience and a audio engineer. Now I am finishing my Graduate studies for Entertainment Business. I have a Bachelor's Degree in Recording Arts from Full Sail University and I look forward to what life has in store for me in the next years.
What is The Summing Amp?
The Summing Amp is an interactive blog especially for audio engineers and audiophiles in general. I hope everyone who visits will receive something from the blog, but it is geared for professionals in the audio and entertainment industries. I wish to "sum" the information I have in my person and find in my studies onto one stream for my followers. I also wish to have my followers interact with me and the other followers, sharing information and tricks of the trade. I wish most of all to reach the best and the brightest of the industry and share my love for recording, performing, and producing entertainment of many different mediums.